Restoring Structural Integrity: Tiling Damaged Beams in Southern Europe
In many parts of Southern Europe, it is not uncommon to encounter structural beams that have suffered from rust and other forms of damage, compromising their integrity. However, with the right approach and specialized products, these beams can be effectively repaired and restored to their former strength.
Assessing the Damage and Seeking Professional Advice
Before embarking on any repair work, it is crucial to have the damaged beams assessed by a qualified structural engineer or architect. They will be able to provide guidance on the extent of the damage and the most appropriate course of action to ensure the safety and stability of the structure.
Preparing the Surface for Tiling
Once the necessary repairs have been made, the next step is to prepare the surface for tiling. This typically involves cleaning the beams thoroughly to remove any rust or debris, and treating them with a suitable rust inhibitor or other protective coating as recommended by the structural engineer or architect.
Choosing the Right Tile Adhesive
When it comes to selecting a tile adhesive for this type of application, it is essential to choose a product that is specifically designed to meet the demands of the environment and the substrate. One such product is Sopro MEG 667, a silver-grey, highly flexible, sag-resistant, rapid-set, two-component, cementitious tile adhesive that meets the C2 FTE S2 requirements of DIN EN 12004.
Key Features and Benefits of Sopro MEG 667
Suitable for wall and floor installation of stoneware, fully vitrified stoneware, natural stone, and cast stone units
Stress-relieving effect of mortar matrix allows application to young concrete substrates and newly laid, unheated cement screeds (tiles with max. 60 cm edge length) and wall and floor heating constructions
Particularly suitable for outdoor use, e.g., on balconies and patios, and applications where the adhesive system is subject to enhanced flexibility requirements
Suitable for facades, steps/stairways, and swimming pools
Suitable for large-format units with edge length not exceeding 120 cm on walls, outdoors
Very high saponification resistance and flexibility
High, long-term frost resistance due to very low water absorption
By following a structured approach that involves professional assessment, thorough surface preparation, and the use of a high-performance tile adhesive like Sopro MEG 667, it is possible to restore damaged structural beams in Southern Europe and create a durable, long-lasting tiled surface that meets the demands of the environment and the substrate.
For installation of earthenware, stoneware and fully vitrified stoneware tiles, ceramic split tiles, clinker floor tiles, mosaic, discoloration-resistant natural stone units, cast stone units and terracotta coverings. For facades, residential, commercial and industrial facilities, swimming pools and for laying large-format units.
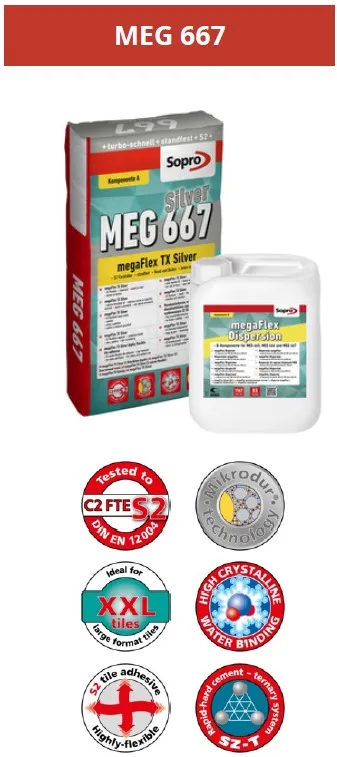
Substrate shall be clean, solid, strong, dimensionally stable and free from any adhesion-impairing substances. Fill any existing cracks in screed with structurally bonding Sopro SH 649 shaken resin. Level out any gross irregularities using Sopro RAM 3 454 renovation and levelling mortar or Sopro RS 462 repair filler; for floors, use Sopro FS 15 550 floor-levelling compound, Sopro VS 582 self-levelling filler or Sopro FS 5 549 floor-levelling compound. Metal substrates (indoors only) shall be dry, clean, solid, strong, rigid, of adequate dimensional stability and free from any adhesion-impairing substances. Metal substrates shall also be pretreated with Sopro HPS 673 bonding primer to provide continuous, full-cover coat, which shall then be allowed to dry properly. Corrosion-prone metal surfaces shall be pretreated as necessary. In addition, all relevant standards, guidelines and recommendations shall apply; workmanship shall comply with good practice. Where Sopro MEG 667 is used, newly laid (unheated; floating or unbonded) cement screeds are ready for tiling as soon as they are walkable and for up to max. 5 days (tiles with edge lengths not exceeding 60 cm) after laying, provided they are adequately strong and meet the requirements of DIN 18 560. Screeds shall be protected against premature drying out prior to commencement of tiling. Concrete substrates (min. 28 days old) shall have a solid surface and be free from mould oil residue and any other adhesion-impairing substances. Where required, concrete shall be mechanically pretreated. Screeds incorporating Sopro Rapidur® B1 rapid-set screed binder are ready to receive tiles after only 12 hours, Sopro Rapidur® B3 after 1 – 2 days, and Sopro Rapidur® B5 after 3 days. Calcium sulphate (anhydrite and self-levelling anhydrite) screeds shall be adequately ground, vacuum-cleaned and primed, and shall exhibit moisture content ≤0.5% CM for unheated and ≤ 0.3% CM for heated constructions. Gypsum plasterwork shall be dry, single-coat and shall not be felt-floated or smoothed. Cement and calcium sulphate screeds incorporating heating elements shall be heated up to ensure adequate drying out prior to flooring installation. Here, cement screeds shall exhibit residual moisture ≤ 2.0% CM. Particleboard/chipboard shall be laid in a staggered
pattern, with glued tongued and grooved joints and additionally screwed down; it shall be rigid, and dry before and after laying. Where timber substrates offer inadequate rigidity (e.g. old floorboards), required dimensional stability of the base may be achieved by laying Sopro FDP 558 tile insulation board. All relevant standards, guidelines and recommendations shall apply; workmanship shall comply with good
practice.
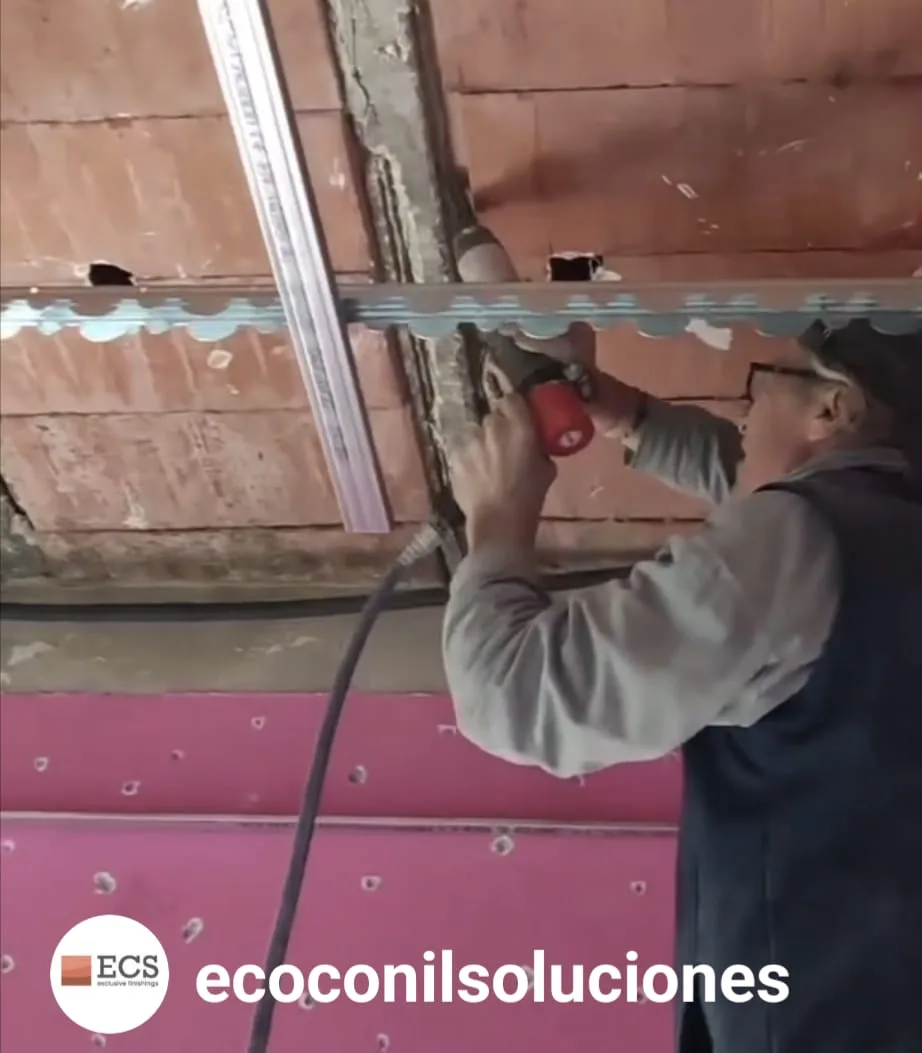
Fill a clean container with Component B mixing liquid, add 25 kg Sopro MEG 667 Component A and mix thoroughly by machine to lump-free consistency. After 3 – 5 minutes of maturing time, remix thoroughly. An extra max. 0.75 ltr water (for 25 kg container) may be added to extend the open time (time up to skinning) in unfavourable weather conditions, e.g. strong sunshine or heavy wind. Water can be added to soften the original sag-resistant consistency, sag resistance is thus reduced. Apply contact layer with finishing trowel, then apply combed bed with a suitable notched trowel (tool angle approx. 60°). Apply only as much adhesive as can be covered by tiles during open time (approx. 45 minutes). Press tiles firmly into the adhesive bed, position and align. Rake out joints before hardening and washing down the covering. Note: Powder Component A must not be used without Component B mixing liquid. Component B mixing liquid shall not be used in conjunction with other Sopro thin-bed or medium-bed adhesives or other mortars.
We are currently collaborating with or actively testing more than 20 brands that align with our rigorous standards.