Common Building Issues:
As homeowners or professionals in the construction and real estate industries, you will encounter a wide range of building issues that can impact the safety, functionality, and longevity of properties. These challenges can arise at any stage of a building’s lifecycle, from design and construction to ongoing maintenance and renovations. In this article, we’ll provide an overview of common building issues and perspectives on addressing these challenges. We’ll cover topics such as structural integrity concerns, mechanical and electrical system malfunctions, envelope and weatherproofing issues, and the challenges of maintaining an ageing infrastructure.
Structural Integrity Concerns
One of the primary areas of focus when it comes to building issues is the structural integrity of the property. This can encompass a wide range of concerns, from foundation problems and load-bearing issues to concerns about the overall structural soundness of the building.
Envelope and Weatherproofing Challenges
The building envelope, which includes the roof, walls, windows, and doors, plays a crucial role in protecting the interior from the elements. Issues with weatherproofing, insulation, or the integrity of the envelope can lead to a variety of problems, such as water intrusion, energy inefficiency, and comfort concerns.
Maintenance and Aging Infrastructure
As buildings age, the need for ongoing maintenance and the potential for infrastructure deterioration becomes increasingly important. This can include everything from the gradual wear and tear of building materials to the need for upgrades or replacements of aging systems and components.By understanding the common building issues outlined in this neutral overview, professionals can better prepare for and address the challenges that may arise in their work. This knowledge can inform decision-making, guide preventative maintenance strategies, and help ensure the long-term viability and success of any construction or real estate project.
Door frame cracks
There are a few common reasons why cracks can form between a metal door frame and a concrete wall:
Settling and shifting of the building structure over time. As a house settles, the concrete wall and metal door frame may not move together perfectly, causing a gap to open up between them. This is a normal part of a house “settling in” and is not a major structural concern if the cracks remain small.
Improper installation of the door frame. If the metal frame was not properly shimmed and secured to the concrete wall during installation, it may not be perfectly flush against the wall, leading to small gaps. Door frame installers need to leave a small 3mm (1/8″) gap between the frame and wall to allow for slight settling.
Expansion and contraction of materials. The metal door frame and concrete wall expand and contract at different rates with changes in temperature and humidity. Over time, this can cause a gap to open up between them. Applying a flexible caulk or sealant in the crack can help accommodate this movement.
Concrete shrinkage. As concrete cures and dries, it can shrink slightly, pulling away from the door frame and creating a crack. This is most common with new construction.
In most cases, these cracks are minor cosmetic issues that can be easily filled and closed with a cork based elastic paint after filling with caulk or joint compound and repainted. However, if the cracks are large, growing, or accompanied by other signs of structural issues, it’s best to have a professional inspect the area to ensure there are no underlying problems with the foundation or framing. But in general, small cracks between a metal door frame and concrete wall are a normal part of a building’s settling and ageing.
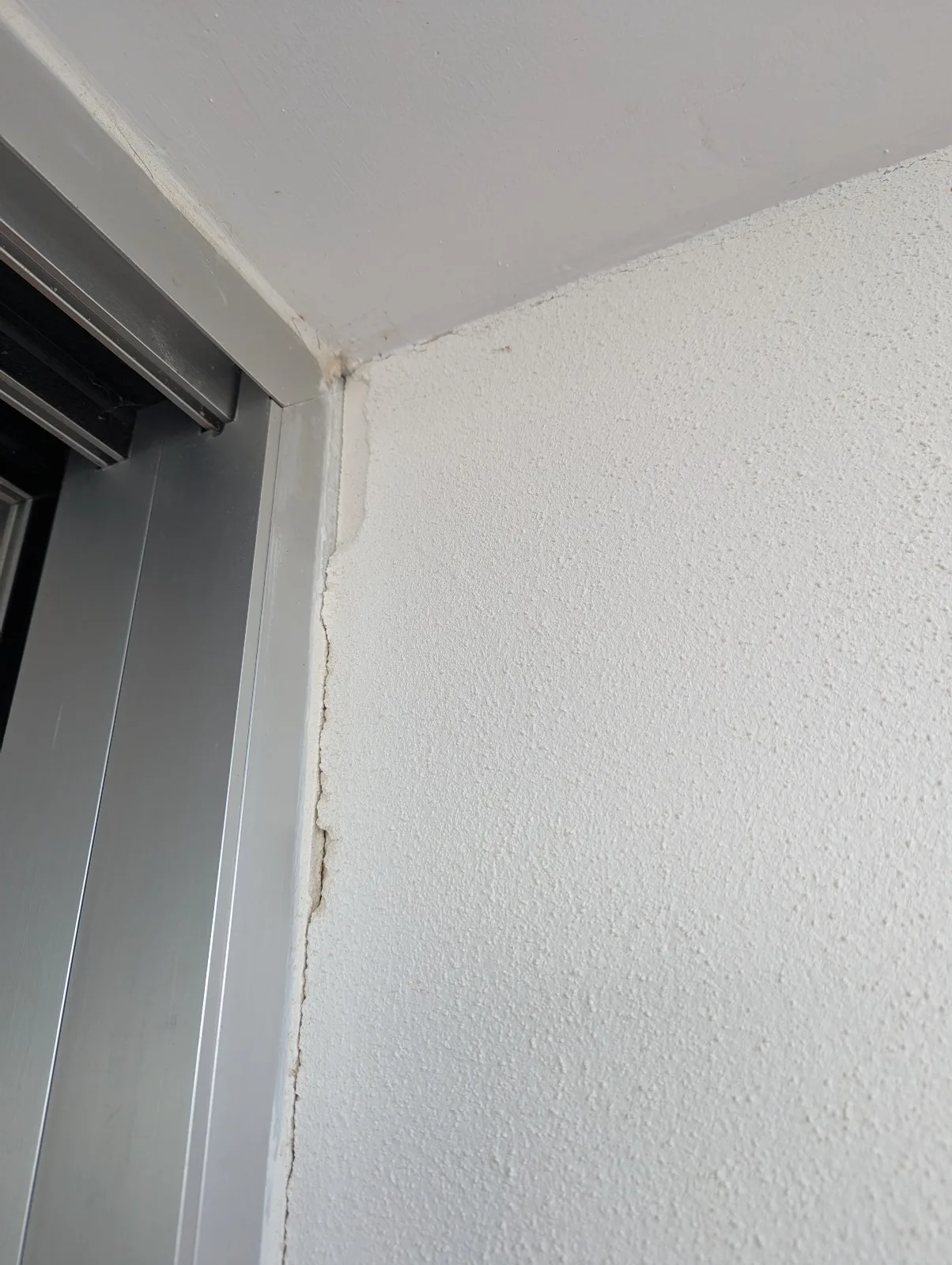
Ring beam cracks
Cracks above a ring beam are often a sign of structural settling or foundation movement. A ring beam is a reinforced concrete beam that is built around the perimeter of a building, typically at the top of the foundation walls or at the base of the walls. As the building settles over time, the differential movement between the ring beam and the walls above it can cause cracks to form.
These cracks are typically horizontal or diagonal in nature, and may appear above door or window openings where the structural stresses are concentrated. The cracks are often wider at the top, indicating that the wall above the ring beam has shifted downward relative to the beam.
Settling cracks above a ring beam can be a sign of more serious foundation issues, such as soil subsidence, reactive soils, or poor initial construction. They should be monitored closely, as continued movement could lead to further structural damage. A structural engineer should be consulted to assess the cause and severity of the cracking and recommend appropriate remediation measures, which may include underpinning the foundation or installing a piled raft system.
It is however recomended that a structural engineer take a look.
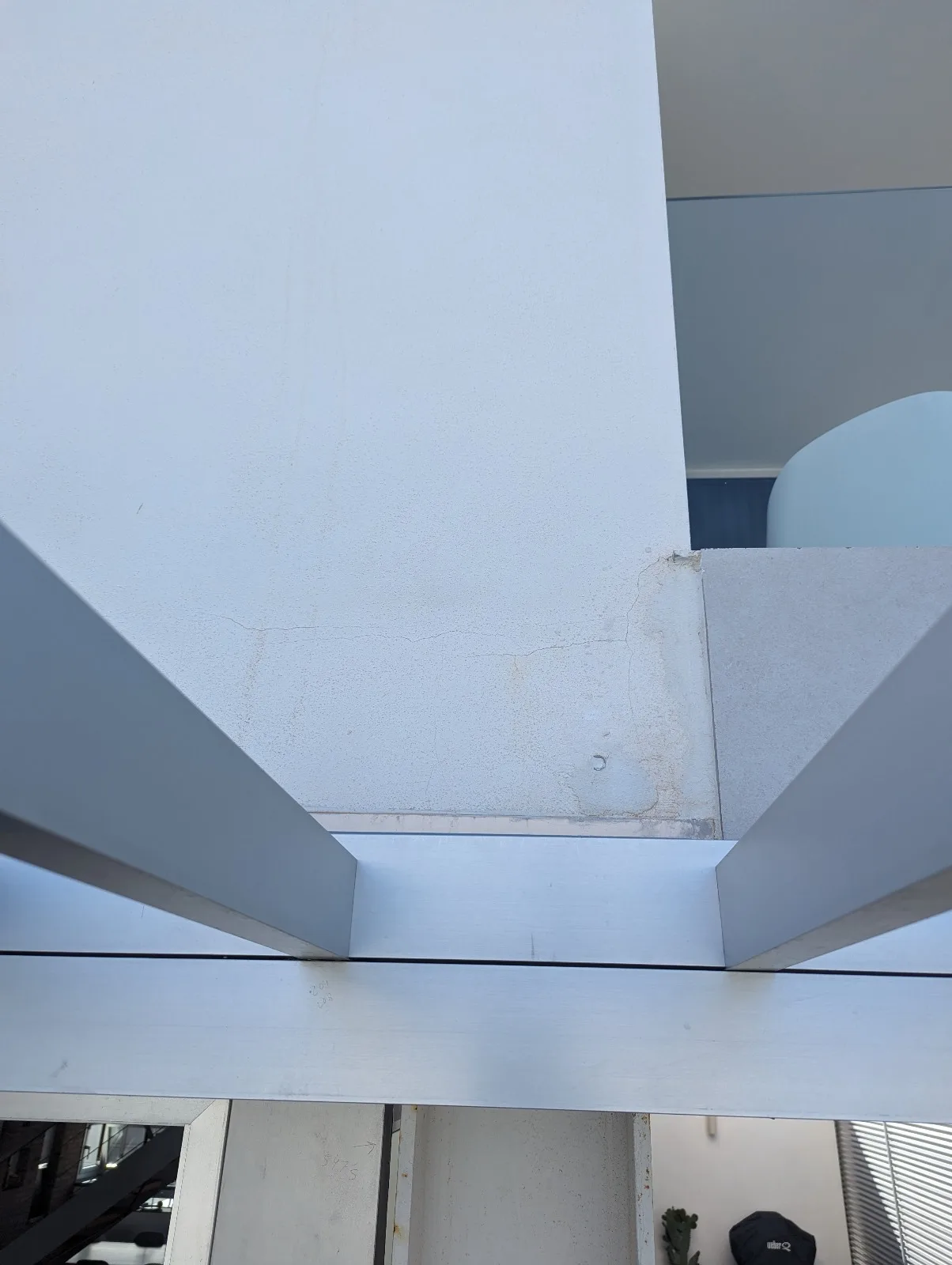
Flat roof area tanking
Taking a look at these photos, it appears that asphalt has been used. It also appears that it has not been tanked and needs to be clarified with the architect who can normally provide a tanking certificate from the installer.
Tanking a flat roof refers to the process of waterproofing a flat roof to prevent water ingress and leaks. The key points are:
- Tanking involves creating a waterproof tanking membrane – A plastic or rubber sheet membrane (Normally EPDM) that is installed over the roof deck to provide a waterproof layer.
- The purpose of tanking is to protect the roof structure and the interior of the building from water damage. Flat roofs are more prone to water ponding and leaks compared to pitched roofs, so proper waterproofing is crucial.
- Tanking is especially important for flat roofs on below-ground structures like basements and cellars, where the roof is surrounded by earth and subject to high water pressure and moisture.
- Ensuring a durable, long-lasting waterproof barrier for a flat roof requires meticulous preparation of the roof deck, careful sealing of edges and penetrations, and precise installation of the tanking system in strict accordance with the manufacturer’s specifications – this includes extending the waterproofing membrane to cover all areas under any retaining wall tiles. Comprehensive coverage is critical to safeguard the membrane from potential damage caused by UV exposure and penetration.
It is also the opinion of many experts, that the only product that should be used in Mediterranean climates for tanking is EPDM.
there are a few key reasons to use EPDM roofing over asphalt:
- Durability: EPDM rubber roofing membranes can last up to 50 years, while asphalt shingles typically only last 15-30 years. EPDM is highly resistant to UV rays, ozone, and weathering.
- Waterproofing: EPDM provides superior waterproofing protection compared to asphalt. It is a single-ply membrane that is less prone to leaks and water infiltration. The seams can be sealed for a completely watertight roof.
- Ease of Installation: EPDM is easier and faster to install than asphalt shingles, especially on low-slope roofs. It can be adhered with a cold-applied adhesive rather than requiring hot asphalt.
- Sustainability: EPDM is considered a more environmentally friendly option than asphalt. It does not contain hazardous materials like asbestos that were commonly used in older asphalt roofing. EPDM is also recyclable at the end of its lifespan.
- Versatility: EPDM can be used on a variety of roof types, including flat, low-slope, and even sloped roofs. It is suitable for both residential and commercial applications[5]. Asphalt is more limited to steep-slope residential roofs.
- Cost-Effectiveness: While the initial cost of EPDM may be higher, its longer lifespan and lower maintenance requirements make it more cost-effective over the long run compared to asphalt.
In summary, EPDM provides superior durability, waterproofing, ease of installation, sustainability, versatility and cost-effectiveness compared to traditional asphalt roofing, making it an excellent choice for many roofing projects.
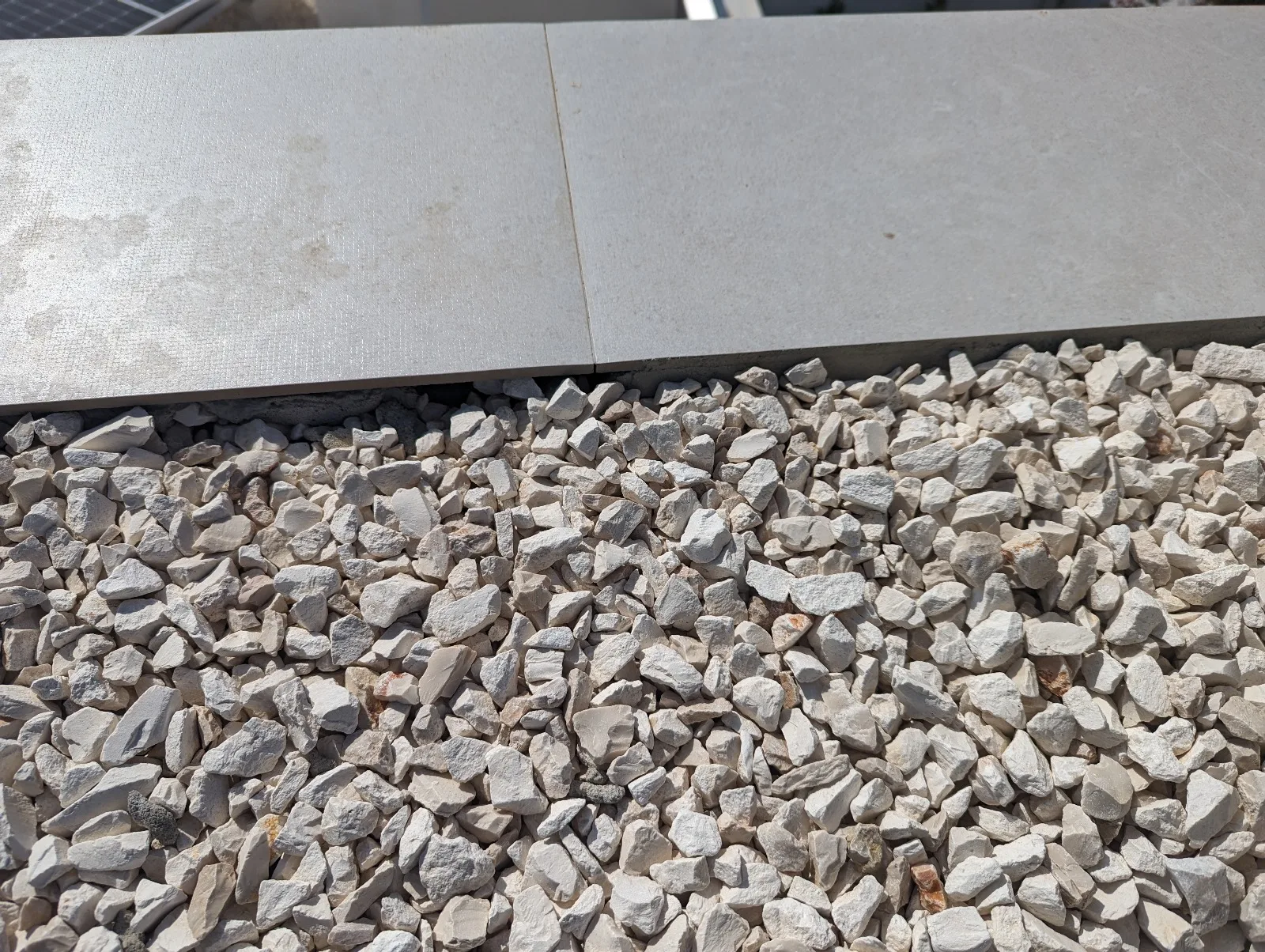
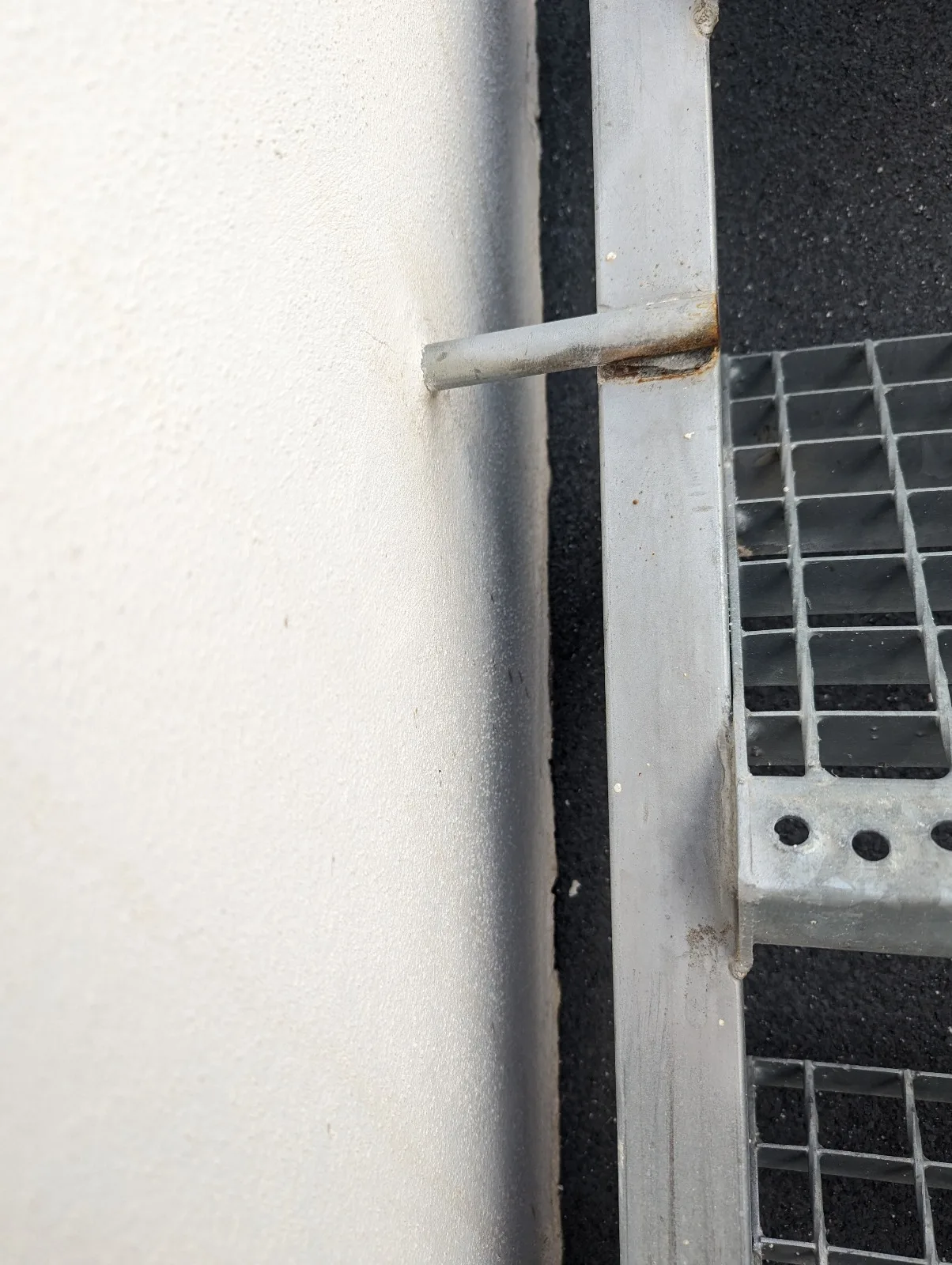
Common reasons why walls develop cracks
Thermal expansion and contraction: Changes in temperature cause building materials to expand and contract, creating stress that can lead to cracks, especially along joints and corners.
Moisture damage: Water seeping into walls through leaks, cracks or condensation can cause materials to swell, warp or rot, resulting in cracks. Moisture damage is more common in walls exposed to high humidity.
Foundation settlement: Shifting, sinking or eroding soil beneath the foundation causes it to move or crack, which is noticeable in walls directly connected to the foundation
Structural damage: Damage or deterioration of structural elements like beams and columns can cause walls to sag, bow or crack, especially load-bearing walls.
Poor quality materials or workmanship: Substandard materials or improper installation techniques can lead to cracks, peeling or crumbling of walls.
Shrinkage: New drywall or plaster can develop tiny zig-zag cracks as it dries out.
Vibrations: Heavy traffic, equipment or objects striking walls can cause cracks that radiate out from a central point.
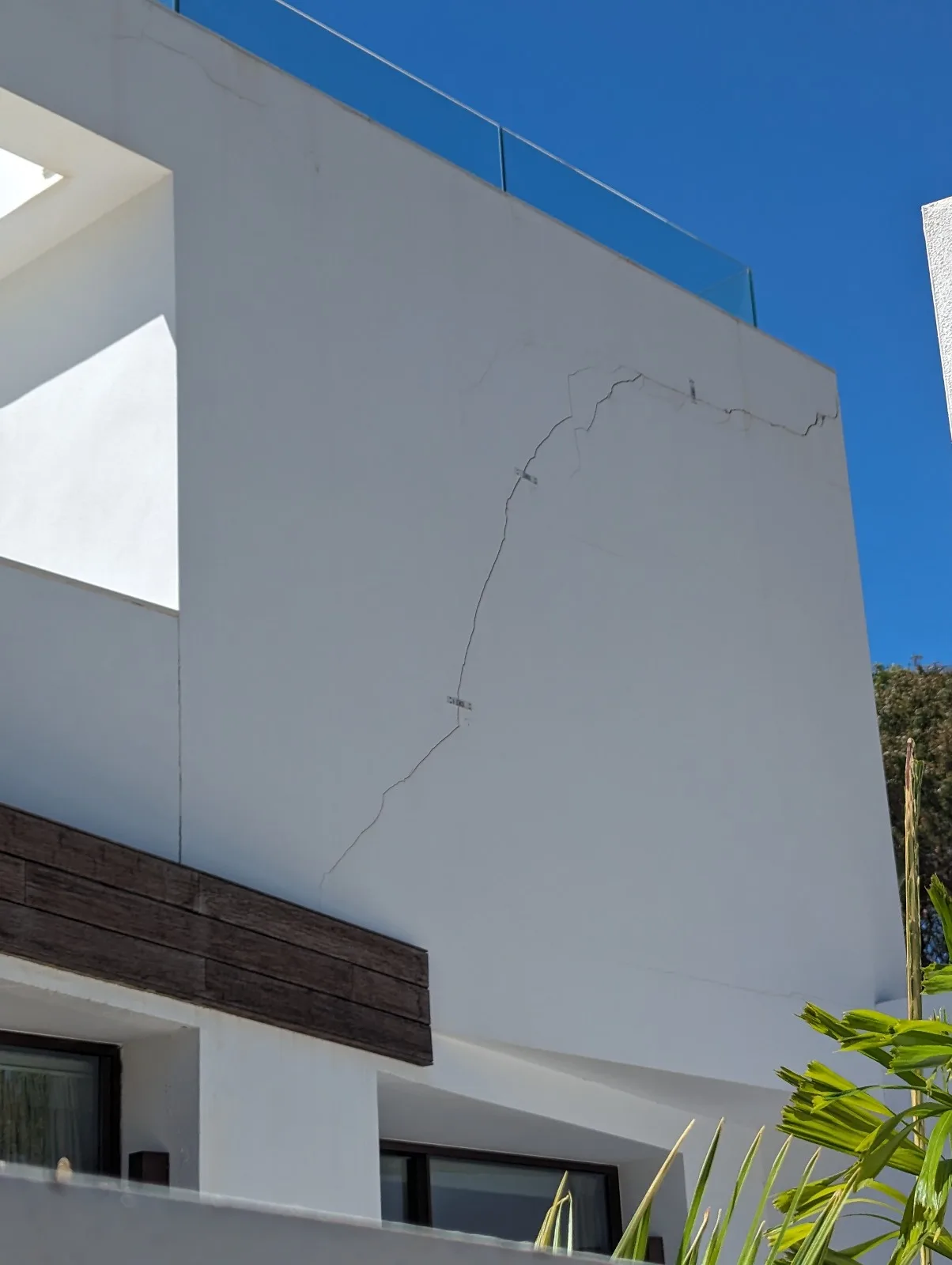
Premature rusting
Premature rusting of metal supports and gates is a common issue that can significantly impact the structural integrity and lifespan of these critical components. Corrosion, caused by exposure to moisture, chemicals, or environmental factors, can lead to the deterioration of metal surfaces, resulting in weakened structural members and compromised functionality. To mitigate this problem, proper material selection, protective coatings, and regular maintenance are essential.
It is well within reason to expect 10 to 15 year guarantee on all metal work on a property when new. The most durable metal coatings are generally considered to be:
- Galvanization: Galvanized coatings can last 20-50 years depending on environmental factors. The lifespan is influenced by factors like coating thickness, surface preparation, and maintenance.
- Powder coating: Powder coatings can last 15-25 years in normal outdoor environments. They provide excellent resistance to corrosion, impact, and UV radiation.
- Electroplating: Electroplated coatings like chrome, nickel, and zinc can last 5-20 years depending on the plating thickness and environmental conditions. Proper surface preparation is key.
- Liquid Metal Anodizing (Type 3): Type 3 anodized aluminium coatings are very durable, with a lifespan of 15-25 years in typical outdoor conditions. They offer good wear resistance.
The ISO 12944 standard categorizes coating durability into four ranges:
– Low (L) – Less than 7 years to first major maintenance
– Medium (M) – 7-15 years
– High (H) – 15-25 years
– Very High (VH) – Over 25 years
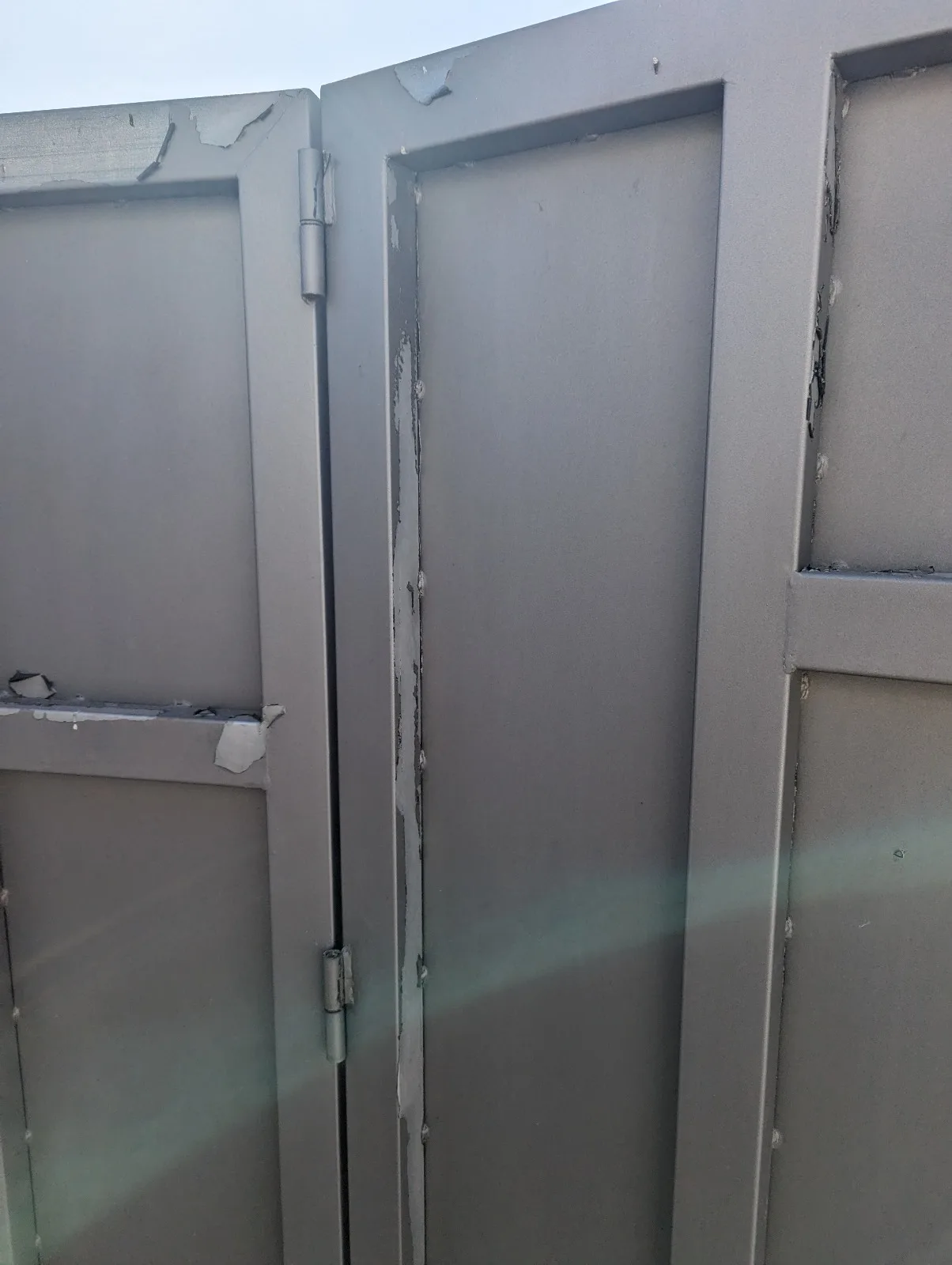
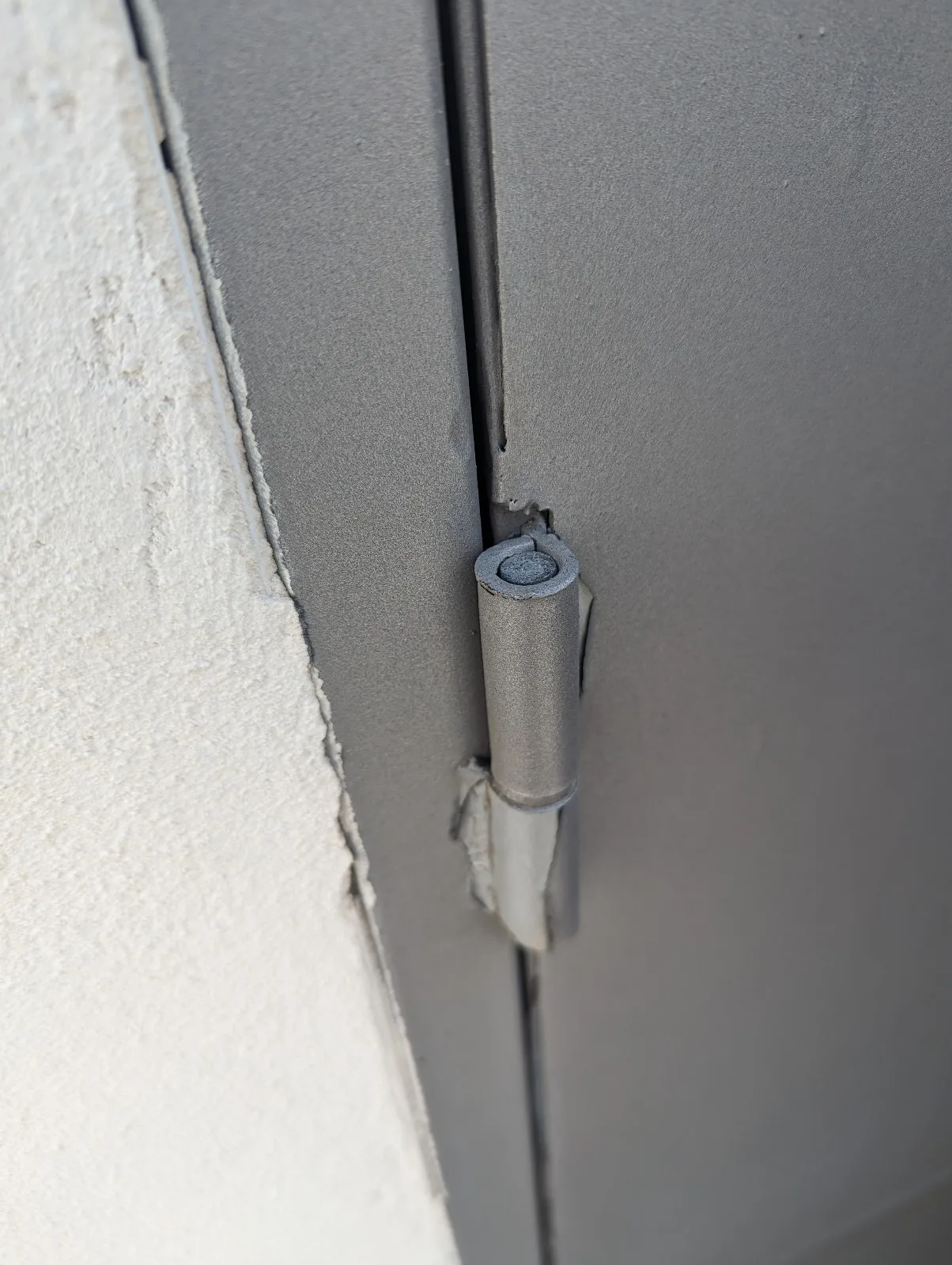
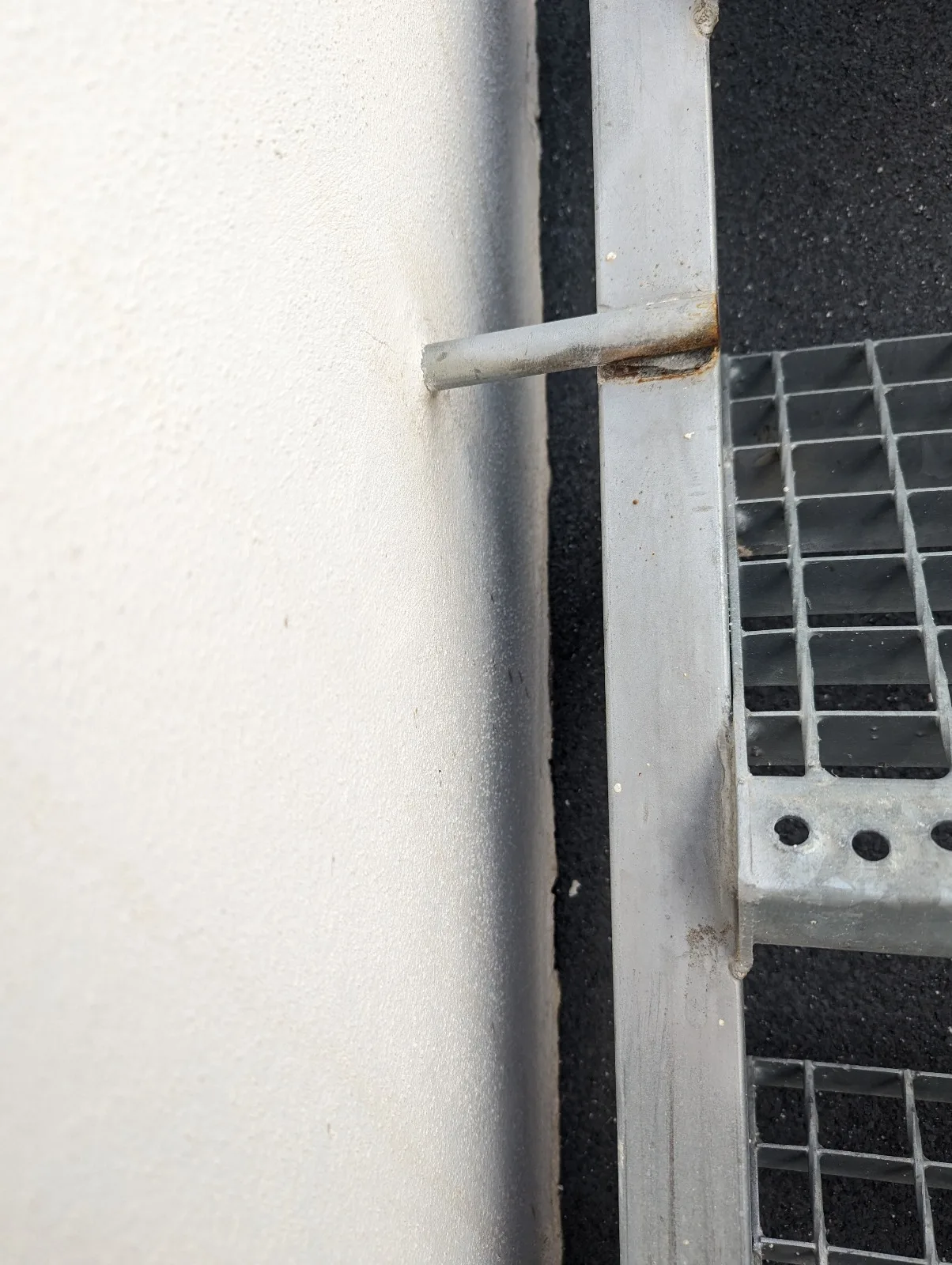
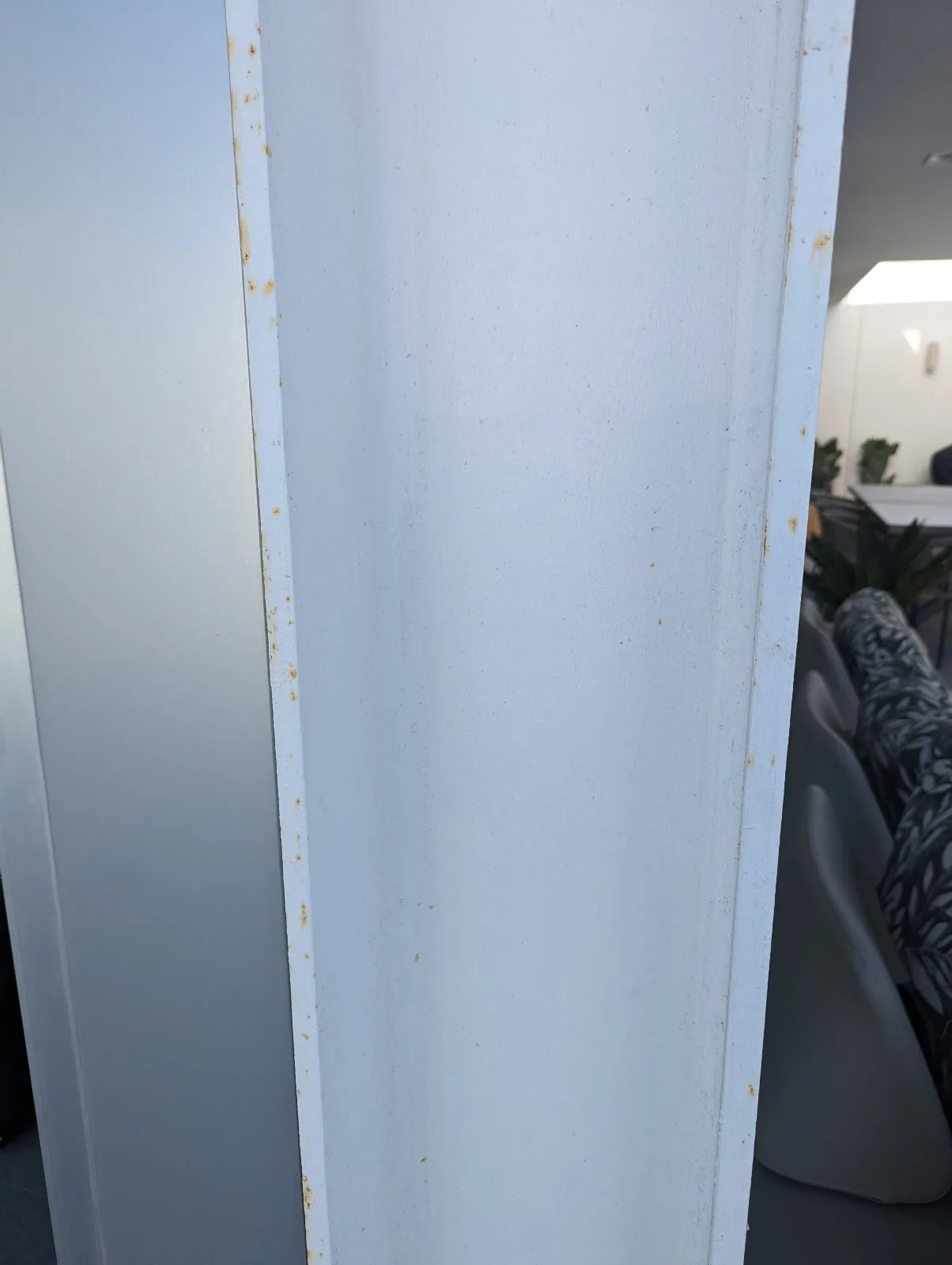
As we get time we will add more.